Performance Impacts of Metal Additive Manufacturing of Very Small Nozzles
Document Type
Article
Publication Date
2021
Abstract
For small satellite electrothermal or chemical thrusters, nozzle throat diameters may be less than 1 mm. At these sizes, the effects of flow surface roughness on nozzle performance must be considered. In this research, nozzles were processed using a nickel alloy by laser powder bed fusion (LPBF), a form of additive manufacturing. Experimentally, the thrust coefficient was measured over a range of targeted throat Reynolds numbers and nozzle expansion ratios. Additional nozzles were manufactured using traditional machining practices to compare performance at similar flow conditions. An analytic model was then developed to determine that performance may not be predicted by traditional viscous loss theory. Surface features of the LPBF manufactured nozzles appear to have caused bow shock systems that overwhelm all other impacts, limiting performance of the as-printed nozzles. This imperfection was then implemented into a computational fluid dynamics (CFD) flow study, showing shock wave reflections and similar thrust losses.
DOI
10.1061/(ASCE)AS.1943-5525.0001229
Source Publication
Journal of Aerospace Engineering
Recommended Citation
Tommila, C. D., Hartsfield, C. R., Redmond, J. J., Komives, J. R., & Shelton, T. E. (2021). Performance Impacts of Metal Additive Manufacturing of Very Small Nozzles. Journal of Aerospace Engineering, 34(2), 04020115. https://doi.org/10.1061/(ASCE)AS.1943-5525.0001229
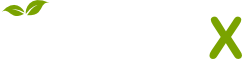
- Citations
- Citation Indexes: 5
- Usage
- Abstract Views: 22
- Captures
- Readers: 20
- Mentions
- News Mentions: 1
Comments
This is an open access article published by the American Society of Civil Engineers as cited below, and distributed under the Creative Commons Attribution License, which permits unrestricted use, distribution, and reproduction in any medium, provided the original work is properly cited. CC BY 4.0